“Sustainability” in textiles refers to the use and refinement of environmentally friendly methods in the production of fabrics. This means establishing practices that conserve energy and natural resources and minimise negative environmental, economic, and social effects.
A “sustainable fabric” is one produced in a way that reduces environmental effects through recycling of water and raw materials, heat recovery from wastewater and steam generation, reduction of dye and chemical usage, and substitution of chemicals.
Sustainability begins with the design of the product, which takes into consideration the choice of fibre, yarn, fabric, dye, fabric finishing, and garment processing. Manufacturers employing sustainable practices in denim dyeing enjoy the following benefits:
• Improved brand reputation and customer satisfaction among environmentally concerned garment producers, retailers, and consumers.
• Reduced costs, through decreased use of dyes, chemicals, and energy and decreased wastewater treatment costs.
This report discusses issues related to sustainability in denim dyeing and presents the results of a study on sustainability sponsored by Cotton Incorporated. As part of this study, denim producers and suppliers of machinery and chemicals for denim production were surveyed about methods they have implemented that demonstrate the potential for reducing water use, energy use, or raw-material waste. Surveys were distributed to hundreds of denim professionals worldwide, who were asked to provide information on such topics as consumption of water, steam, indigo and sulfur dyes, and reducing agents, and on yarn waste. In addition, denim companies were asked to participate by conducting trials using methods that have been reported to improve sustainability, quality, and efficiency by reducing dye consumption, using chemical products that reduce chemical oxygen demand in wastewater, and improving washing techniques while reducing water consumption.
Survey Responses and Trial Results
Responses to the surveys regarding levels of resources produced a wide range of answers. Water consumption was unknown or ranged from 2 to 20 L/kg of yarn. Indigo dye on weight of yarn ranged from 1.4% to 6% for essentially the same depth of shade, and similar ranges were reported for sulfur bottoms, sulfur tops, and 100% sulfur blacks. In trials of improved washing methods, water consumption was reduced by 60% to 80%, yarn breaks on sheet ranges were reduced by 40% to 50%, re-beaming efficiency on rope dyeing machines was increased by 30% to 40%, and warp stops in weaving were greatly reduced. Additional responses from denim mills are mentioned throughout this report as applicable to specific aspects of sustainability in denim dyeing.
Overview of Indigo Dyeing
Although many colours of denim are offered, most denim is yarn-dyed with indigo. Indigo dyeing is one of the most difficult and complicated of all dyeing methods, involving complex chemical reactions, repeated dye applications, and challenges in shade control. The sulfur dyes used for dyeing denim yarns also pose technical challenges.
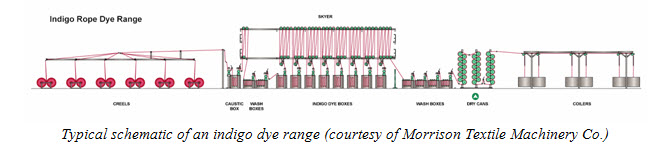
Before the application of indigo dye, the yarn is pretreated. The most common pretreatments are sulfur bottoming, scouring with sodium hydroxide, and causticizing. Sulfur bottoming involves pretreatment with sulfur dyes (either black alone or a combination of blue and black), which reduces the amount of indigo needed to produce a dark shade, thus reducing cost. Scouring with sodium hydroxide involves applying sodium hydroxide at low concentrations (< 5%) and high temperatures (> 85°C) to remove impurities in cotton, such as waxes, pectins and minerals that would interfere with indigo dyeing and result in streaks. In causticizing, sodium hydroxide is applied at sub-mercerization concentrations (< 18%); this pretreatment affects depth of shade and colourfastness.
Sulfur dyes account for approximately 25% of dyes used on indigo dye ranges; the remaining 75% consists of indigo and other vat dyes. For indigo and sulfur dyes to penetrate cotton fibres, they must be made water soluble through a vatting process, in which the dye undergoes chemical reduction. This typically requires the use of a reducing agent that is activated with an alkali. The most commonly used reducing agents are sodium hydrosulfite (Na2S2O4, CAS No. 7775-14-6, more correctly identified as sodium dithionite) for indigo dyeing and sodium sulfide (Na2S, CAS No. 1313-82-2) for sulfur dyeing. Reduction is followed by oxidation to re-form the pigment in situ and develop the final colour. Indigo dyeing is best understood as a form of chemical engineering with three basic ingredients: indigo, the alkali sodium hydroxide, and the reducing agent sodium hydrosulfite. When these are combined, an array of by-products appears in the dye bath, including several forms each of indigo, alkali, and reducing agents. Monitoring of indigo dyeing requires special procedures and careful interpretation of the data for correction of dyeing issues.
Sustainability in Indigo Dye Production
The source of natural indigo dye is the plant Indigofera tinctoria. Natural indigo has long been used as a colorant for food, cosmetics, hair, paint, and fireworks, as well as a dye for textiles. However, nearly all indigo dye produced today is synthetic.
Some efforts to promote sustainability in indigo dyeing and the manufacture of denim jeans have involved campaigns by brands based on consumer demand for natural or all-organic jeans. Some styles are produced with organic cotton and/or natural indigo dyes. However, evaluations by DyStar Textilfarben GmbH have found that natural indigo and organic cotton are not available in sufficient quantities to meet the market’s demand. DyStar has also shown that the natural indigo dyestuff production process in total (considering land requirements, harvesting, dye extraction, and residual biomass) is less environmentally favourable than optimised indigo synthesis.1
The manufacture of indigo dye has rarely resulted in injuries or significant environmental damage. Indigo is easily removed from wastewater and poses no hazards when disposed of properly. Modern synthetic indigo production incorporates purification processes to ensure the quality of the dye, which reduces the amount of chemicals required during the dyeing process. However, indigo synthesis does require the use of non-renewable materials, primarily phenylglycine, the manufacture of which consumes large quantities of aniline.
Dye suppliers have developed offerings of pre-reduced liquid colorants that provide significant environmental advantages by eliminating problems of handling the reducing agents, controlling the reduction process, and managing the reaction by-products (such as hydrogen sulfide). An eco-efficiency analysis conducted by BASF (now DyStar) comparing dyeing methods and use of natural and synthetic indigo found that the optimal eco-balance in the production of indigo blue jeans was achieved through the use of pre-reduced synthetic indigo and the electrochemical dyeing process.2
DuPont has established a manufacturing base that synthesizes indigo from a sugar-type compound via a microbial process that mimics natural biosynthesis of indigo. Research is continuing on genetic modification of bacteria to produce indigo more efficiently. However, biosynthetic indigo currently costs several times as much as conventional synthetic indigo and therefore has attracted little interest from the denim industry.3
Decreased Use of Indigo Dye
An obvious way to reduce indigo consumption is to use less of it in dyeing. The traditional method of indigo ball warp dyeing results in ring dyeing (surface dyeing) of the yarn. Processing conditions can vary greatly among dye ranges, resulting in differences in dye penetration into the yarn. The degree of penetration affects the colour yield; less penetration of dye into the yarn will produce a darker colour with the same amount of indigo.
The degree of penetration depends on the solubility of the dye, with lower solubility producing darker colour. Solubility is determined by the pH of the dye; dyeing at pH 11 produces a much darker shade than dyeing at pH 12 with the same amount of indigo.
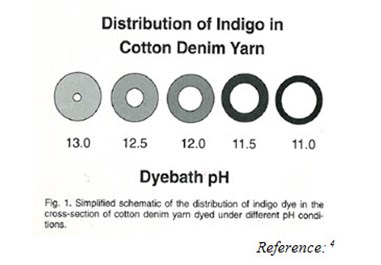
However, indigo dyeing at lower pH results in problems with consistency, because sodium hydroxide in low concentrations becomes unstable at the low temperature. To achieve adequate dye solubility at lower pH, buffers have long been used. The most common pH buffer is potassium carbonate, the use of which reduces indigo requirements for dark shades by an average of 30%.5 This method results in increased surface dyeing, which also has the benefit of reducing machine time and chemical usage for garment fading by up to 50%.
Lowering the reduction potential of the dyebath also allows the same depth of shade to be produced with much less indigo. Using a reduction potential of –780 mV and 2% indigo dye in the dyebath typically will produce a shade depth equivalent to that resulting from dyeing at a reduction potential of –800 mV or higher with 4% indigo or more. Dyeing at a lower reduction potential also greatly decreases the amount of sodium hydrosulfite required.
Decreased Use of Reducing Agents
The reducing agents sodium hydrosulfite and sodium sulfide are consumed in massive quantities for denim dyeing and are the most significant contributors to chemical oxygen demand (COD) in denim textile dyeing effluent. COD is an indirect measure of the amount of organic compounds in water; it measures the mass of oxygen consumed by oxidization of these pollutants in one litre of solution (expressed as milligrams per litre or parts per million). When organic compounds are discharged into water, high consumption of oxygen can be lethal for aquatic life. The COD of sodium hydrosulfite is around 210 mg/L; the COD of sodium sulfide was not readily available.
The health effects on workers using these sulfur-based reducers can be significant.6,7 Exposure to sodium sulfide can result in eye and skin irritation or corneal damage. Exposure to sodium sulfide can cause skin, eye, and respiratory tract irritation and allergic reactions. If the pH of sodium sulfide in solution falls to 7, the sodium sulfide decomposes to release toxic hydrogen sulfide gas, which can be recognised by its characteristic “rotten egg” odour. Exposure to hydrogen sulfide gas at low concentrations can irritate the eyes, nose, and throat. Brief exposures to higher concentrations can result in loss of consciousness and in some cases long-term effects such as headaches and neurobehavioral effects. Prolonged exposure to high concentrations can result in potentially fatal pulmonary edema. Generation of hydrogen sulfide gas can be avoided by adequate washing to remove sulfides from yarn before it enters oxidation boxes or other baths that contain acids.
Alternatives to Sulfides
The most commonly used environmentally friendly alternative to sulfides in sulfur dyeing of denim are reducing sugars, such as glucose, dextrose, and molasses. Reducing sugars have no odour, very low COD, and no adverse effects on the health of workers. Some brands of liquid sulfur dyes arrive already reduced with sugars instead of sulfur-based reducers, which, especially for sulfur blacks, greatly reduces problems with sulfides.
A recent innovation for reduction of sulfur dyes is the use of hydrogen gas, which not only eliminates most of the reducing-agent load, but also allows shipping of pre-reduced dye at a higher concentration (40%) and higher reduction potential, which results in superior wash-fastness.8 This method of dye reduction has long been used for pre-reduced liquid indigo, which eliminates the need for sodium hydrosulfite in dye mixes but does require a supplemental hydrosulfite feed to the dye boxes. Once the dyeing is complete, the hydrogen gas reacts with oxygen in the air, producing only water as a by-product.
Alternatives to Sodium Hydrosulfite
Thiourea dioxide has often been suggested as a more environmentally friendly alternative to sodium hydrosulfite, because of its lower toxicity and higher stability. Less thiourea dioxide is required for reduction; however, it is more expensive than sodium hydrosulfite. At this time, no denim operations have been identified that are using thiourea dioxide in indigo yarn production, though it is used by many US indigo craft and garment dyers.9
During World War II, a shortage of zinc for production of sodium hydrosulfite caused US indigo dyers to return to the earlier process of using molasses as a reducing sugar for indigo dyeing. One kilogram of molasses was shown to generate the same levels of reduction as one kilogram of sodium hydrosulfite, as a 100% replacement or employed in blends with hydrosulfite.10
Microbial reduction of indigo in fermentation vats is a centuries-old process by which carbohydrates (such as bran starch) are allowed to ferment naturally, as in wine production, producing hydrogen. One project to reintroduce this process for indigo dyeing is currently under way in the United States.11
Electrochemical methods for reduction of indigo, in which electrodes are used to generate hydrogen from water, are easily demonstrated in the laboratory. In a demonstration by an indigo supplier using a small pilot range with five small indigo dye boxes, the yarn was successfully dyed. However the cost of installing the system even on a very small machine was reported to be prohibitively expensive.12
Additional reductions in water, energy, and chemical use may be achievable through the use of alternative reduction chemistry, such as sodium borohydride, which can be more efficient than sodium hydrosulfite and have less impact on water quality in terms of COD and total dissolved solids.
Decreased Consumption of Reducing Agents
An obvious way to reduce the pollution generated by the reduction process, as well as the cost of dyeing, is to use less reducing agent. In the case of sodium sulfide, excessive amounts are sometimes applied, up to 75 g/L, where only 15 g of a high-quality product are necessary to achieve the optimal reduction potential. Laboratory testing should be conducted to determine the minimal amount of sodium sulfide required to reach a reduction potential of approximately –590 mV.
In the case of sodium hydrosulfite, consumption per kilogram of indigo ranges widely, from 120%, which should be adequate, to 400%. A problem with the use of sodium hydrosulfite is that it is easily oxidized by atmospheric oxygen, especially at the surface of the dye boxes. Once mixed with water and alkali, sodium hydrosulfite begins to decompose in the dye boxes and also in the stock mix.
Technically, its loss is related to the specific surface area of the dye liquor, which is the ratio of the surface area exposed to the air to the total volume of dye in the box. The half-life of sodium hydrosulfite loss (the time required for 50% to be lost) is inversely proportional to the specific surface area. Depending on the design of the dye boxes, 15% to 50% of sodium hydrosulfite is lost, with the highest surface losses occurring in the lowest-volume dye boxes.
Several methods are available to reduce surface loss of sodium hydrosulfite during dyeing. One is the use of nitrogen blankets on the dye box surface, to prevent oxygen from contacting the dye. This method has proven to be cost-effective on indigo loop dyeing machines used in Latin America, which have only a single indigo dye box (compared with five to eight boxes in other machine designs). One company reported placing ping-pong balls on the dye box surface to block atmospheric oxygen.
Losses of sodium hydrosulfite from the stock mix also are significant. Its initial concentration in stock mixes can range from 60 to 120 g/L. At the higher concentrations, the losses are greatest, with the concentration dropping to as low as 30 g/L because of solubility limitations and losses from atmospheric oxygen during stirring. These losses can be greatly reduced by limiting the initial concentration in the mix to 80 g/L. Losses can also be limited through the use of a reductive buffer, which is a second reducing agent added to protect the hydrosulfite from oxidation. Preferably, reductive buffers containing sulfur are used, such as sodium thiosulfate or sodium hydrosulfide.
Decreased Use of Chemical Auxiliaries
In addition to indigo, sodium hydroxide, and sodium hydrosulfite, the majority of denim operations use wetting agents, sequestering agents, dispersants, softeners, fixatives, oxidisers, acids, sulfur dyes, and sulfur dye reducers. These products add to the cost of dyeing, are generally from non-renewable sources, can contribute to pollution, and sometimes are used in excessive quantities with minimal benefit.
Wetting Agents and Dispersants
Wetting agents (surfactants) are used to reduce the surface tension of a liquid, allowing improved penetration of fibres, uniformity of application, and/or higher washing efficiency. One end of a surfactant is attracted to water and the other end to particles, allowing the water to transport the particles into or out of fibres.
In denim wet-processing, anionic surfactants (with a net negative electrical charge) are used, generally in the scouring stage. The surfactants used are generally sulfate, sulfonate, phosphate, or carboxymethylate esters, at 2.0 g/L. If anionic surfactants are not adequately washed off the yarn before it enters the indigo dye boxes, streaking or uneven dyeing can result. Also, these surfactants will react with sodium hydrosulfite, affecting the reduction potential. Except in production of light indigo or sulfur colours or in situations where colourfastness of dark colours needs improvement, there is little advantage to using surfactants in denim dyeing. Indigo dyeing machines have extraordinarily large dye boxes relative to the quantity of yarn in the box, and the machines operate at lower speeds than in any other type of continuous dyeing. Therefore, wetting agents are of minimal value for accelerating wetting. In pre-wetting, hot (> 85°C) sodium hydroxide alone sufficiently reduces the surface tension to remove waxes, pectins, fats, and organic colour.
When mercerizing concentrations of sodium hydroxide (20% to 25%) are employed in pre-wetting, products known as mercerizing penetrants, usually higher alcohol sulfates, are used. However, at mercerizing concentrations of sodium hydroxide, water becomes bound to the hydroxide in the form of a hydrate, so the water is not free to combine with the penetrant. Therefore, the use of penetrants offers no improvement in wetting (wet pickup) and results in economic waste and pollution when they are washed out. Ordinary alcohols (isopropyl alcohol, methanol, or butanol) are effective in reducing the surface tension of mercerizing liquors at much lower cost; they are also renewable and have no environmental impact, because they vaporise during yarn drying.
Indigo dye dispersants are commonly added to stock mixes produced with powder dye. However, this usually is not necessary, because indigo suppliers add adequate levels of dispersing agent to their products. If a dye dispersant is needed, an effective alternative is sorbitol. This renewable sugar alcohol is made from natural products, unlike synthetic dispersants, which are often based on lignin sulfonates or sodium formaldehyde-sulfoxylates.
Sequestering Agents
Sequestering agents, also known as chelating agents, are compounds that form complexes with metal ions in solution, thus negating the effect of hardness (the presence of metals or alkaline earth salts) in water and fibres on dyes, wetting agents, and oxidizers. Anionic surfactants generally are deactivated by hardness. In situations where anionic surfactants are used in production of light colours, a small amount of an ethylenediaminetetraacetate (EDTA) sequestering agent improves dyeing results. Although sequestering agents are often added to indigo mixes, they are unnecessary, because of the reducing power of hydrosulfite. In denim operations, organophosphonic acid sequestering agents are most commonly used; however, these only disperse hardness, which is of minimal benefit in dyeing.
Acids
Acids are used in denim dyeing to neutralise mercerized yarn and for chemical oxidation of sulfur dyes. Acetic acid, which is most commonly used, has a high COD, is irritating to humans and toxic to microorganisms used in water treatment, and reacts with alkalis to produce sodium acetate, which affects the softness of cotton. Citric acid, a renewable product synthesised from glucose, is often used as a safe alternative; however, it is a much weaker neutraliser than acetic acid and is generally more expensive. The safest, most economical acid for pH control and neutralisation is carbonic acid. Carbonic acid is produced by passing carbon dioxide gas through water. Control is simple, by means of a feedback loop with a pH meter. In the past, a few textile operations have produced carbonic acid by capturing hydrocarbon-produced gases from steam boilers.
Softeners
On indigo rope dyeing machines, a softener is usually applied in the last box as an aid to yarn rebeaming. However, optimal results are obtained through improved washing and moisture control after drying, rather than application of a softener. Dirty yarn is an important cause of high weaving breaks in denim, because chemicals not washed from the yarn after indigo dyeing result in bad sizing and lower protection of warp yarns. Because wash boxes on rope ranges are typically more efficient than the smaller wash boxes on sheet ranges, use of chemical softeners can be avoided.
Sulfur Dyes
Sulfur dyes are applied on yarns as a foundation colour (bottom) before indigo dyeing or as a top colour after indigo dyeing. After the sulfur dye is applied, a significant amount of the dye is removed during washing, and 40% to 70% of the removed dye enters waste streams. Most of this waste is from the use of sulfur black dyes. Loss of sulfur dyes is the second most important source of water contamination in denim dyeing, after sodium hydrosulfite, and represents a needless economic loss and waste of non-renewable resources.
These dye losses result in part from the use of low-quality sulfur dyes (especially powders) and inexpensive, low-efficiency reducing agents (especially sodium sulfide). Other factors resulting in sulfur dye loss are excessively high pH (> 11) in dyeing and hot washing immediately after dyeing. The most significant problem in the efficient application of sulfur dyes on indigo dyeing machines is pH control. Sulfur black dyes are often applied at pH 13 to 14, which can result in a large portion of the dye being wasted. Using sodium bicarbonate buffer to lower the pH to 11 eliminates most dye waste. That, along with air oxidation and initial cold washing, has resulted in 100% utilisation of the dye, no loss of dye in washing, and reduction of sulfur dye costs by at least half.
Decreased Water and Steam Consumption
In indigo dyeing, process water is used for scouring, dyeing, and washing, and steam is used for heating liquids and drying. Modern wash boxes use counter flow, with the yarn and liquid moving in opposite directions, to reduce water usage and increase energy efficiency. Drain amounts from wash boxes are typically in the range of 30.4L/min.
Water used for steam in the drying section is expelled as condensate collected from the dyeing cylinders after the heat from steam is absorbed in drying the yarn. This water, at least 1 L/kg of yarn, has the potential to be reused, but recovery would be relatively expensive. High humidity reduces drying efficiency, increasing the steam required per kilogram of yarn, and steam consumption can be greatly reduced by efficient removal of humidity from around drying sections. Other ways to reduce steam consumption are to repair steam leaks (which can cost $10 to $15 per hour), to replace inoperable steam traps, and to renovate inefficient drying cylinders that have low heat transfer.
Waste of low-pressure steam is significant on indigo dyeing machines, especially sheet dyeing machines. After heat transfer, significant amounts of steam escape along with the liquid condensate. Morrison Textile Machinery Company, of Fort Lawn, SC, has introduced a process for the utilization of lost steam. The system consists primarily of a condensate tank and a steam compressor, which is aligned with a standard set of 12 drying cylinders. Morrison projects that this system will significantly increase energy efficiency, with payback periods of 4.2 months for oil (based on a price $0.59/L) and 5.8 months for natural gas.13
The application of sulfur dyes on indigo dyeing machines usually requires temperatures of about 90oC, which requires enormous amounts of steam. As a general rule, the amount of steam required doubles with each 10oC increase in process temperature. Indigo Blue, of North Augusta, SC (the author’s company), has pioneered energy-efficient methods for sulfur dyeing, including dyeing with sulfur black dye at a temperature of 30oC.
Recovery of Indigo
If the dyeing process is not controlled properly, a large amount of indigo can be removed in washing; the wasted indigo then enters wastewater streams. This wastage generally results from the use of excessive concentrations of indigo in the boxes (> 3 g/L) or low sodium hydrosulfite concentrations. The wasted indigo consists of (1) indigo that was not reduced to the leuco form and (2) indigo that was reduced but did not attach to cotton fibre. The unreduced indigo has the potential for recovery and reuse for cotton dyeing. The indigo that was reduced but did not attach to cotton has lower colour yield when re-reduced.
Indigo can be removed from the waste by flocculation and/or absorption in the sewage sludge and can be recycled via ultra-filtration. A traditional method for recovering indigo is to add aluminium sulphate to the wash water, precipitating the dye, and then dissolving the precipitate to release the dye. Recycling of indigo dye from the waste stream by ultra-filtration is aided by use of the vibratory shear enhanced process, a vibration technology designed to prevent membrane fouling. Another approach employs palygorskite clay to absorb the indigo, followed by conversion of the recovery by-products into Maya Blue, an organic-inorganic hybrid pigment with applications in the paint and coating industry.14
Recycling of Waste Yarn
Sheet dyeing machines are required to stop when the warp yarns terminate, which occurs on average twice a day. As a result of the stoppage, the quality of the yarn in the machine from the entry to the drying section through sizing is too low for processing into fabric on modern high-speed weaving machines. The length of yarn wasted ranges from 600 to 1,000 m. However, this yarn can be used in handloom weaving, which produces a truly vintage appearance, often favoured in high fashion. This method of reusing indigo-dyed yarn waste is being used on a limited scale in South Asia.
Innovations in Machinery and Process Design
IndigoGenius
Several years ago, the Master Company, of Macherio, Italy, introduced a significantly different indigo dyeing machine under the IndigoGenius brand. Based on the continuous slasher dyeing technique, the machine was designed for greater economy and reduced environmental impact in indigo dyeing. It uses only two or three indigo dye boxes in a closed-circuit inert environment in which higher-than-normal concentrations of indigo are used at higher-than-normal temperatures. The company projects significantly lower energy consumption, 80% less hydrosulfite consumption, much lower water consumption, and reduction of yarn wastage.15
Advanced Denim
The Archroma Advanced Denim concept (introduced by Clariant Chemicals several years ago) was designed to increase performance and sustainability while expanding the range of denim shades and effects. To achieve the look of indigo denim, this process uses a sulfur dye that approximates the hue of indigo, and allows either solid or ring-dyeing. The Advanced Denim Pad/Sizing-Ox process requires only one dye box, using sulfur dye and a biodegradable sugar-based reducing agent. After intermediate drying, the yarn passes into the sizing box, where it is simultaneously sized, oxidised, and fixed. Compared with conventional indigo sheet dyeing, the process is reported to reduce water consumption by 92%, energy costs by 30%, and waste yarn by up to 87%.16
KG Denim
KG Denim, of Coimbatore, India, has become a leader in sustainability with regard to denim fabric, claiming to offer the most sustainable denim in the world. Like most denim mills, KG is a vertical, or integrated, textile operation, meaning that raw cotton enters the factory and leaves as finished denim fabric. Denim operations typically exercise precise control over greige mill processes like spinning and weaving, but control over the wet processing is typically haphazard. KG Denim has made a significant advance in control over dyeing and finishing, while reducing costs through sustainability initiatives. The company recovers and returns to manufacturing 94% of the process water that leaves dyeing. Of the electrical energy used, 75% is produced by wind farms, and energy consumption has been reduced by means of improved internal lighting, the use of energy-efficient motors, and an energy monitoring system. A humidification system reduces water consumption dramatically, and cotton waste (amounting to 10% of the raw cotton entering the factory) is recycled for use as boiler fuel, replacing non-renewable oil and coal.17
Conclusions and Recommendations
• The issue of sustainability is important to consumers, retailers, and many garment operations, and it has been shown that sustainable practices can improve both profit and customer satisfaction.
• The environmental impact of denim production is devastating in many developing countries. That China’s Pearl River has become a blue-black toxic sewer is a prominent example of the results of dumping untreated denim waste streams into the environment.18 The costs of water treatment are avoided in order to keep the costs of denim products down. Only when the customers of denim producers demand environmental accountability and are prepared to pay a slightly higher price for fabric will this begin to change.
• The garment sector has made advances in reducing environmental impact with methods such as ozone treatments and the use of enzymes to replace non-renewable and hazardous chemicals. Fabric producers can reduce not only environmental impacts but also costs by employing dyeing techniques that reduce indigo consumption. This in turn will reduce energy and chemical consumption in garment fading.
• There is significant interest in reducing the environmental impact of denim dyeing. The primary focus should be on advancing the technology of dyeing and the understanding of the dyes and chemicals in current use. This can be accomplished through existing training programmes on the mechanical and chemical processes involved, which are more complex than for any other dyeing method.
• Finally, organised involvement by all stakeholders, from providers of machinery and materials for indigo dyeing to jeans consumers, will promote environmentally responsible action.
About the Authors
Harry Mercer has been involved in the denim business for 32 years, primarily in the areas of dyeing, finishing, environmental impact, and product development. He previously worked for Cone Mills (1980–1986), Swift Denim (1989–1991), and the Graniteville Company (1991–1994) and served as the Laboratory Manager for The American Association of Textile Chemists and Colorists (1986–1989). For the last 18 years, he has consulted with over 50 denim companies in 18 countries. Mr. Mercer has published 23 articles on indigo dyeing, sulfur dyeing, denim finishing, and stretch fabrics. He is widely recognised as one of the world’s leading authorities on denim manufacturing.
R. Michael Tyndall is currently vice-president of Product Development and Implementation for Cotton Incorporated. He began his career there in 1974 beginning in the product testing laboratory, moving on to product development and then into technical services. He is a Chartered Colorist Fellow with the Society of Dyers and Colorists and is the immediate past President of The American Association of Textile Chemists and Colorists. Cotton Incorporated is the non-profit organisation representing America’s cotton producers and importers.
Sources
1. DyStar Textilfarben GmbH.
2. Saling, P., et al., Eco-efficiency analysis by BASF: the method. International Journal of Life Cycle Assessment 7:203–218, 2002.
3. Scott T. Brix, Director of Marketing, DuPont Industrial Biosciences, Beloit, WI, personal communication, 2012.
4. J. Noland Etters, Textile Chemist and Colorist, Vol. 27, No 2, February 1995.
5. Peter Hauser, Professor of Textile Engineering, Chemistry, and Science. North Carolina State University School of Textiles, Raleigh, NC, personal communication, 2012.
6. U.S. National Library of Medicine, Hazardous Substances Data Bank, http://toxnet.nlm.nih.gov/cgi-bin/sis/htmlgen?HSDB, Record for Sodium hydrosulfite, last updated June 3, 2010, Record for Sodium sulfide, last updated February 14, 2013.
7. Agency for Toxic Substances and Disease Registry, Public Health Statement for Hydrogen Sulfide, July 2006. http://www.atsdr.cdc.gov/PHS/PHS.asp?id=387&tid=67.
8. Hebei Rising Chemical Co., LTD, Shijizhuang, Hebei, China.
9. Jane Palmer, Owner, Noon Design Studio and Natural Dye House, Los Angeles, CA, personal communication, 2012.
10. American Association of Textile Chemists and Colorists, The Application of Vat Dyes, AATCC Monograph No.2, p. 230, 1953.
11. Nicholson, S.K., and John, P., The mechanism of bacterial indigo reduction, Applied Microbial and Cell Physiology 68:117–123, 2005.
12. Alexander Bock, Director, Bluconnection Pte. Ltd., Singapore, personal communication, 2012.
13. Peter Parker, Director of Engineering, Morrison Textile Machinery, Fort Lawn, SC, personal communication, 2012.
14. Wambuguh, D., and Chianelli, R., Indigo dye waste recovery from blue denim textile effluent: a by-product synergy approach. New Journal of Chemistry 32:2189–2194, 2008.
15. Master S.R.L., Macherio, Italy.
16. ICIS Innovation Awards 2012: Clariant offers a greener blue denim. http://www.icis.com/Articles/2012/10/22/9605427/icis-innovation-awards-2012-clariant-offers-a-greener-blue.html.
17. Srihari Balakrishnan, Managing Director, KG Denim Ltd., Coimbatore, India, personal communication.
18. Chang, E., China’s famed Pearl River under denim threat. CNN, April 28, 2010, http://www.denimsandjeans.com/environment/denim-pollution-in-xintang-the-blue-jean-capital-of-the-world